Dans un environnement professionnel de plus en plus volatile et concurrentiel, comprendre les causes profondes des difficultés rencontrées est devenu un impératif stratégique. Qu’il s’agisse de dysfonctionnements dans la chaîne logistique, de retards dans un projet, ou encore de problèmes qualitatifs, identifier la racine du problème est la clé pour concevoir des solutions durables. La méthode des 5 pourquoi, simple en apparence, s’impose comme un outil incontournable pour dénouer les nœuds complexes qui paralysent souvent les entreprises. Issue du système de production Toyota, elle permet d’aller au-delà des symptômes et de remonter méthodiquement à l’origine des perturbations.
Dans le contexte actuel, où des sociétés majeures telles qu’Airbus, L’Oréal ou Capgemini cherchent à optimiser leurs processus tout en renforçant leur agilité, cette approche structurée contribue à décupler l’efficience opérationnelle. En explorant notre article, vous découvrirez comment déployer cette méthode à travers des exemples concrets issus de secteurs variés, ses limites, ainsi que les conseils d’experts pour l’adapter à votre organisation.
Une démarche progressive, rodée grâce à des pionniers comme Toyota et enrichie par des groupes internationaux tels que Dassault Systèmes ou Saint-Gobain, fait de ce questionnement incessant un levier puissant pour piloter la performance et l’innovation.
Décryptage de la méthode des 5 pourquoi : comprendre sa mécanique et sa finalité
La méthode des 5 pourquoi est une technique itérative d’analyse causale qui vise à identifier la racine d’un problème en posant successivement la question « Pourquoi ? ». Cette approche est née dans l’industrie automobile japonaise, précisément chez Toyota, où la rigueur dans la résolution des problèmes est synonyme de qualité et d’efficacité. Le constat est simple : souvent, les solutions se concentrent sur des symptômes visibles qui, sans traitement de leurs causes sous-jacentes, réapparaissent ou génèrent de nouvelles difficultés.
Typiquement, la méthode recommande d’interroger cinq fois la raison d’un dysfonctionnement pour qu’à chaque étape la réponse soit une explication plus profonde, évitant ainsi les analyses superficielles.
Par exemple, si Renault observe un retard dans la production d’un véhicule, la chaîne d’interrogations pourrait ressembler à :
- Pourquoi le véhicule est-il en retard ? — Parce que la pièce A n’est pas arrivée.
- Pourquoi la pièce n’est pas arrivée ? — En raison d’un retard du fournisseur.
- Pourquoi le fournisseur a-t-il pris du retard ? — Problèmes logistiques internes chez lui.
- Pourquoi ces problèmes logistiques existent-ils ? — Mauvaise gestion des priorités dans son entrepôt.
- Pourquoi la gestion des priorités est-elle mauvaise ? — Absence de procédures claires et automatisées.
Ce cheminement démontre qu’un simple problème de retard cache souvent une organisation perfectible. L’identification précise des causes profondes permet ainsi d’adopter des mesures efficaces, telles qu’un partenariat renforcé avec le fournisseur ou l’implémentation d’outils digitaux pour la gestion des stocks.
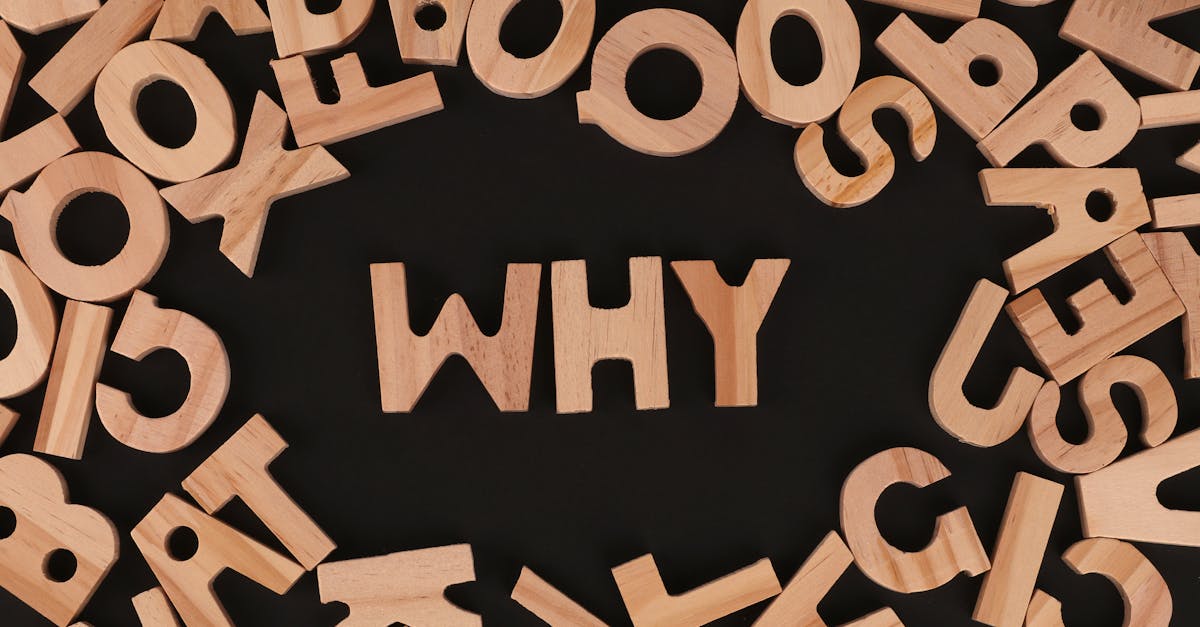
Étape | Question Pourquoi | Réponse attendue |
---|---|---|
1 | Pourquoi le problème est-il survenu ? | Identification symptomatique immédiate |
2 | Pourquoi cette cause est-elle survenue ? | Explication sous-jacente plus profonde |
3 | Pourquoi cette sous-cause est-elle présente ? | Facteurs organisationnels ou humains |
4 | Pourquoi ces facteurs existent-ils ? | Processus ou systèmes inadéquats |
5 | Pourquoi ces processus posent problème ? | Cause racine liée à l’environnement ou à la culture d’entreprise |
Ainsi, cette méthode évite l’écueil de la correction temporaire et encourage une approche rigoureuse d’amélioration continue indispensable dans les entreprises modernes.
L’origine historique et la diffusion mondiale de la méthode des 5 pourquoi
La méthode des 5 pourquoi trouve son origine dans les années 1930 avec Sakichi Toyoda, inventeur et fondateur de Toyota. Face à la nécessité d’améliorer ses processus de production, il insista pour que les équipes interrogent systématiquement la cause des dysfonctionnements par un questionnement en profondeur. C’est ainsi qu’elle s’inscrivit dans le Toyota Production System (TPS), modèle aujourd’hui étudié et repris par les entreprises du monde entier.
Au fil des décennies, cette technique s’est diffusée dans des secteurs variés tels que l’industrie aéronautique où Airbus l’utilise pour garantir la fiabilité, ou encore dans la cosmétique où L’Oréal optimise sa chaîne logistique et son contrôle qualité grâce à ce type d’approche.
Son extension est due à sa simplicité et à son efficacité, mais aussi à son intégration dans des méthodologies plus larges comme Lean, Six Sigma et la roue de Deming. Ces cadres managériaux ont contribué à faire des 5 pourquoi un incontournable pour piloter la qualité et la performance.
- Origine clés : 1930, Sakichi Toyoda, Toyota
- Principaux domaines d’application : automobile, aéronautique, services, distribution
- Intégration : Lean Manufacturing, Six Sigma, amélioration continue
- Diffusion : multinationales telles que Samsung, Capgemini, IBM
L’évolution technique a même conduit à des variantes comme les 5 pourquoi en arborescence, permettant de gérer les problèmes complexes avec plusieurs causes racines, une stratégie adoptée dans des groupes comme Saint-Gobain. L’histoire de cette méthode illustre parfaitement comment une innovation simple peut générer un impact durable à travers le temps et les secteurs.
Pourquoi la méthode des 5 pourquoi est incontournable dans la résolution des problèmes en entreprise
Dans un contexte économique marqué par la pression sur les coûts, les attentes clients exigeantes et la rapidité des cycles d’innovation, disposer d’un outil pragmatique et efficace pour résoudre les problèmes est un avantage compétitif majeur. Alors que certaines entreprises privilégient des solutions ponctuelles, d’autres, comme Danone ou IKEA, investissent dans des méthodes rigoureuses pour pérenniser leurs améliorations.
Les bénéfices principaux de la méthode des 5 pourquoi sont :
- Résolution ciblée : permet d’éviter les doubles emplois et travaux inutiles en s’attaquant à la vraie source des problèmes.
- Réduction des coûts : les erreurs répétées génèrent des pertes évitables, que ce soit au niveau des stocks, des délais ou de la qualité.
- Amélioration continue : favorise la culture d’entreprise apprenante qui analyse systématiquement ses dysfonctionnements.
- Mobilisation des équipes : un questionnement collaboratif engage tous les acteurs impliqués dans le processus.
Prenons l’exemple d’IBM qui a réussi à réduire significativement son taux d’incidents techniques en appliquant cette méthode au sein de ses équipes de maintenance. Chaque incident était systématiquement décortiqué avec cette méthode, ce qui a permis d’identifier des failles récurrentes dans la planification des interventions.
Impact | Conséquence opérationnelle | Exemple d’entreprise |
---|---|---|
Réduction des retards | Amélioration de la satisfaction client | Renault – gestion logistique |
Diminution des défauts | Baisse des coûts de non-qualité | Toyota – contrôle qualité |
Optimisation des ressources | Meilleure allocation des équipes | Capgemini – projets IT |
Renforcement de la collaboration | Meilleure communication interservices | Danone – production |
L’adoption des 5 pourquoi ouvre ainsi la voie à une gestion plus efficace des processus, indispensable pour répondre aux enjeux actuels de compétitivité globale.
Les multiples avantages de la méthode des 5 pourquoi pour les organisations modernes
L’efficacité de cette méthode ne se limite pas à sa capacité à trouver la cause racine. Elle présente un éventail d’avantages qui en font un outil privilégié dans les secteurs industriels comme chez Airbus ou dans les services pilotés par Dassault Systèmes :
- Accessibilité : méthode ne nécessitant pas de compétences techniques pointues, donc utilisable par tous dans l’entreprise.
- Flexibilité : adaptable à une multitude de contextes, qu’il s’agisse d’un souci logistique, d’un problème qualitatif ou d’un défi organisationnel.
- Favorise l’esprit critique : encourage la réflexion et la remise en question des process et comportements.
- Outil économique : ne demande qu’un temps limité pour un impact potentiellement majeur.
Un autre point fort est que cette méthode engage la prise de responsabilité, évitant ainsi que la recherche de coupables ne fasse dérailler la démarche. Elle fonctionne par construction en mode constructif. Par exemple, Saint-Gobain a intégré les 5 pourquoi dans ses audits internes, ce qui a permis d’augmenter le taux de conformité produit tout en dynamisant la collaboration entre les départements production, qualité et R&D.
Avantage | Description | Exemple d’application |
---|---|---|
Simplicité | Méthode intuitive et rapide à mettre en place | IKEA amélioration processus logistique |
Identification des causes | Permet d’aller au fond des problématiques | Toyota et la gestion qualité peinture |
Applicabilité variée | Utilisable en projets IT, production, service client… | Capgemini en gestion de projet |
Économie de ressources | Réduction des coûts liés aux erreurs et défauts | L’Oréal contrôle qualité |
C’est cette conjonction entre rigueur et souplesse qui explique son succès durable sur les cinq continents.
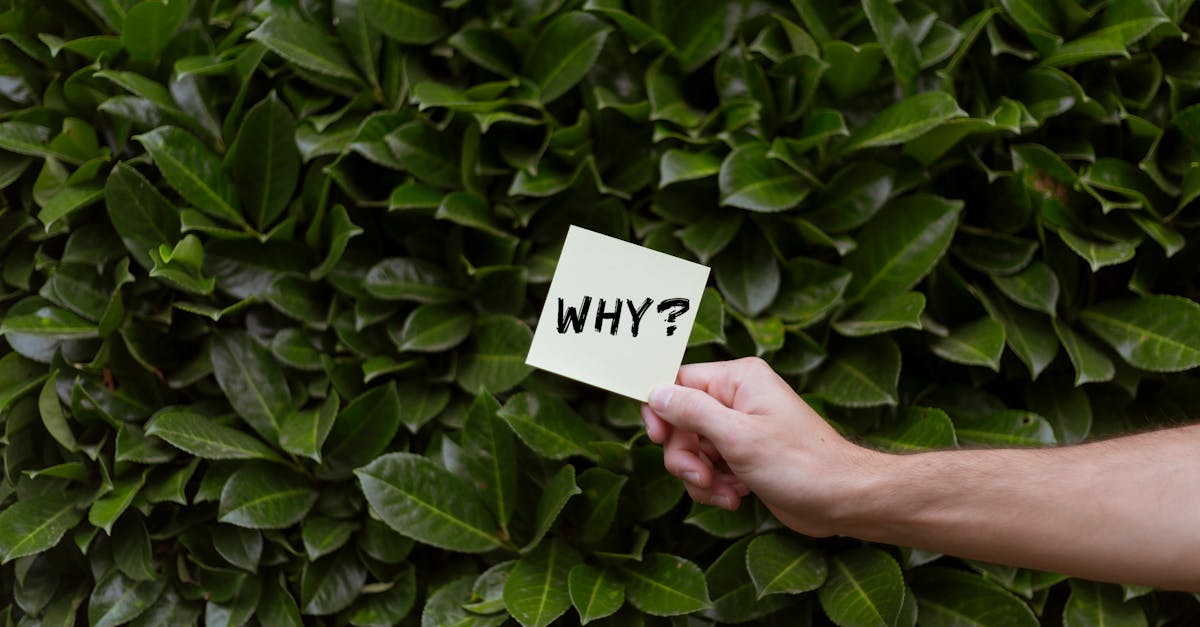
Quand et comment utiliser la méthode des 5 pourquoi dans vos processus opérationnels ?
La méthode des 5 pourquoi se prête particulièrement bien aux situations suivantes :
- Problèmes récurrents : ceux qui apparaissent à plusieurs reprises et nécessitent une analyse en profondeur.
- Situations complexes : où plusieurs facteurs d’impact doivent être démêlés pour découvrir les causes clés.
- Problèmes interdisciplinaires : qui mobilisent différentes équipes et nécessitent une communication fluide et une vision partagée.
Dans une entreprise telle que Danone, où la chaîne de production implique des interactions complexes, la méthode est utilisée pour cerner les défaillances affectant la production ou la distribution, permettant ainsi de limiter les pertes.
Pour garantir un déploiement efficace, voici quelques recommandations :
- Identifier précisément le problème à analyser et le formuler clairement.
- Impliquer toutes les parties prenantes concernées afin d’avoir un panorama large.
- Conserver un esprit ouvert et privilégier les faits plutôt que les opinions.
- Documenter consciencieusement chaque étape de questionnement et réponse.
- S’assurer que chaque question « Pourquoi ? » est pertinente et pousse à aller plus profond.
Type de problème | Objectif de la méthode | Exemple |
---|---|---|
Problème récurrent | Éliminer une cause de façon durable | IKEA amélioration logistique entrepôt |
Problème complexe | Démêler plusieurs causes interdépendantes | Capgemini gestion projet IT multipartenaires |
Problème interdisciplinaire | Faciliter la collaboration et la communication | Airbus gestion qualité production avion |
Dans cette optique, la méthode peut être complétée par d’autres outils comme la matrice SWOT ou les diagrammes de cause à effet, largement détaillés sur Mister Société. De cette manière, le diagnostic s’enrichit et la démarche gagne en précision.
Les étapes clés pour appliquer la méthode des 5 pourquoi efficacement
Une mise en œuvre réussie repose sur un processus structuré et rigoureux. Voici les phases fondamentales :
- Définition claire du problème : sans une formulation précise, l’analyse risque de dévier.
- Observation et collecte des données : pour appuyer les réponses par des faits tangibles.
- Questionnement en profondeur : poser successivement les « Pourquoi ? » en évitant la généralité.
- Évaluation des causes : valider la pertinence de chaque cause identifiée.
- Mise en place d’actions correctives : traduire les enseignements en mesures concrètes.
- Suivi et contrôle : garantir que les solutions adoptées ont un effet durable.
Utiliser un arbre des causes, comme on le fait chez Saint-Gobain, est une excellente manière d’organiser les informations récoltées. Cela permet de visualiser rapidement les relations entre causes et effets. De plus, intégrer une équipe multidisciplinaire renforce la pertinence des réponses et favorise l’appropriation collective des solutions.
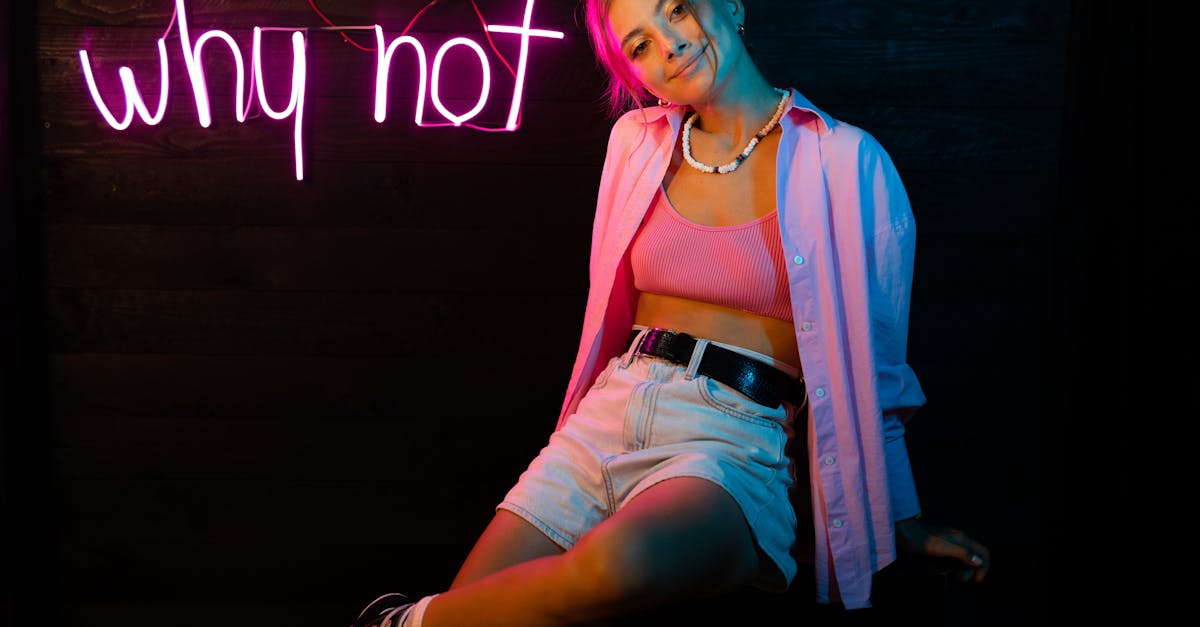
Étape | Description | Conseils pratiques |
---|---|---|
Identification du problème | Formuler le sujet de l’analyse | Rédiger une phrase concise et factuelle |
Recueil d’informations | Collecter données, témoignages, chiffres | Utiliser outils digitaux et entretiens ciblés |
Questionnement itératif | Poser les 5 pourquoi successivement | Impliquer plusieurs points de vue |
Validation des causes | Confirmer la cause racine | Tester avec données et retour terrain |
Actions correctives | Proposer et planifier les solutions | Assigner des responsables et échéances |
Suivi | Mesurer les résultats et ajuster | Réviser périodiquement pour pérennisation |
Exemples d’application concrets et impact sur les performances
Pour illustrer la puissance de cette méthode, voici cinq cas d’usage issus d’organisations renommées :
- Retard au lancement d’un produit chez Danone : l’analyse a révélé que l’absence d’outil avancé de gestion des stocks chez un fournisseur causait un effet domino sur la chaîne logistique.
- Désalignement dans un projet informatique chez Capgemini : un défaut de communication et l’absence de réunion de lancement ont été la cause racine d’échecs dans la coordination.
- Dépassement budgétaire chez une PME industrielle : un effectif inadapté et une sous-estimation initiale de la charge expliquaient la hausse des coûts.
- Hausse des réclamations clients chez L’Oréal : la précipitation dans la production avait dégradé la qualité du contrôle, générant des défauts.
- Défaut de peinture dans l’atelier Toyota : un système de filtration d’air inadéquat expliquait les imperfections constatées.
Ces exemples soulignent l’importance de s’interroger profondément pour ne pas se contenter de traiter les symptômes. En 2025, ces cas sont régulièrement discutés dans les formations en Lean Management ou gestion de projet avancée.
Entreprise | Problème identifié | Cause première | Solution mise en place |
---|---|---|---|
Danone | Retard de livraison produits | Système de gestion des stocks inadapté fournisseur | Implémentation d’outils collaboratifs et audit |
Capgemini | Désalignement équipes | Manque de réunion kickoff | Organisation systématique de lancement projets |
PME industrielle | Dépassement budgétaire | Sous-estimation charge travail | Amélioration du pilotage et revue des prévisions |
L’Oréal | Réclamations clients accrues | Contrôle qualité précipité | Rééquilibrage vitesse/qualité et formation |
Toyota | Défaut peinture | Système filtration air inadéquat | Modernisation des filtres système air |
L’intégration de cette méthode a, dans chacun de ces contextes, permis non seulement de résoudre les problèmes, mais également d’instaurer une dynamique d’amélioration continue plus solide et partagée.
Limites et défis incontournables de la méthode des 5 pourquoi à connaître
Si sa simplicité est un atout, la méthode des 5 pourquoi présente également des limites qu’il convient de prendre en compte pour ne pas minimiser ses résultats :
- Superficialité possible : si les questions sont posées sans rigueur, on peut s’arrêter à des causes peu profondes.
- Subjectivité des réponses : les biais cognitifs ou l’interprétation personnelle peuvent fausser les diagnostics.
- Insuffisant pour les problèmes multifactoriels : certains problèmes complexes nécessitent des approches complémentaires comme l’analyse SWOT ou la méthode 8D, détaillées sur Mister Société.
- Temps et ressources : bien que rapide, la mise en œuvre efficace demande temps et collaboration engagée.
- Risque de recherche de coupables : sans cadre bienveillant, la méthode peut ouvrir la porte à des accusassions non constructives.
Une séance réussie doit être animée par un facilitateur expérimenté, capable de recadrer la discussion et de garantir la neutralité afin d’obtenir un diagnostic pertinent et exploitable.
Limite | Conséquences | Solutions contestées |
---|---|---|
Superficialité des questions | Solutions temporaires inefficaces | Formation à la technique |
Subjectivité | Diagnostic biaisé | Multidisciplinarité des équipes |
Complexité multiple | Causes non exhaustives | Combiné avec d’autres méthodes d’analyse |
Temps de mobilisation | Impossibilité de suivre plusieurs sessions rapidement | Planification et priorisation |
Recherche de coupables | Conflits internes | Culture d’entreprise basée sur la non-culpabilisation |
FAQ sur la méthode des 5 pourquoi : réponses aux questions fréquentes
- La méthode des 5 pourquoi est-elle toujours limitée à cinq questions ?
Non, l’important est d’aller jusqu’à la véritable cause racine. Cinq questions sont un repère, mais il peut en falloir plus ou moins selon la complexité. - Peut-on utiliser cette méthode seul ou faut-il une équipe ?
L’efficacité est renforcée avec une équipe multidisciplinaire qui apporte des points de vue variés. - Quelle différence avec le diagramme d’Ishikawa ?
Le diagramme d’Ishikawa permet de visualiser plusieurs causes à la fois, tandis que les 5 pourquoi creusent une chaîne causale spécifique en profondeur. - Comment éviter les biais subjectifs ?
L’animation doit être neutre, basée sur des faits vérifiables, et encourager la collaboration plutôt que la recherche de coupables. - Quelles sont les alternatives si les 5 pourquoi ne suffisent pas ?
Les méthodes 8D, SWOT ou la gestion des risques sont des outils complémentaires pour les problèmes complexes multi-facteurs.