Dans le monde de la gestion d’entreprise, la maîtrise de la résolution de problèmes est une compétence fondamentale. La méthode 8D, développée initialement par Ford Motor Company, s’impose aujourd’hui comme un processus rigoureux permettant non seulement d’identifier et corriger les problèmes, mais aussi d’assurer leur non-récurrence. Que vous dirigiez une PME, gériez un projet complexe ou souhaitiez garantir la qualité de vos produits, comprendre et appliquer la méthodologie 8D est un atout stratégique pour renforcer la satisfaction client et optimiser la performance de votre organisation. Focus sur cette méthode incontournable pour une amélioration continue durable et un travail d’équipe efficace.
Définition précise de la méthode 8D et son rôle en gestion de projet et qualité
La méthodologie 8D, signifiant huit disciplines, est une approche structurée pour traiter de manière efficace des problèmes, qu’ils soient liés au produit, au processus ou à la satisfaction client. Cette démarche vise non seulement à corriger un défaut, mais surtout à en éradiquer la cause profonde. Le procédé se compose de huit étapes successives :
- D0 : Préparation du processus de résolution, planification des actions nécessaires.
- D1 : Constitution d’une équipe pluridisciplinaire compétente pour traiter le problème.
- D2 : Description détaillée et quantifiable du problème selon la méthode QQOQCCP (qui, quoi, où, quand, comment, combien).
- D3 : Identification et mise en place d’actions immédiates pour limiter la propagation du problème.
- D4 : Analyse approfondie pour identifier les causes racines à l’aide d’outils comme les 5 pourquoi ou diagrammes d’Ishikawa.
- D5 : Définition et validation des actions correctives permanentes alignées sur les résultats des analyses.
- D6 : Mesure rigoureuse de l’efficacité des actions mises en place.
- D7 : Standardisation des nouvelles pratiques pour prévenir toute récidive.
- D8 : Reconnaissance et valorisation du travail de l’équipe.
Dans le contexte professionnel contemporain de 2025, où les exigences normatives telles que l’ISO 9001 ou la norme TS 16949 sont omniprésentes, la méthode 8D offre un cadre robuste pour la gestion de projet et l’amélioration continue. Elle fournit une démarche documentée essentielle à la maîtrise de la qualité et à la satisfaction client durable.
Discipline 8D | Objectif | Outils associés | Responsable général |
---|---|---|---|
D1 | Constituer une équipe compétente | Analyse des compétences, cartographie des ressources | Chef de projet / Leader 8D |
D2 | Décrire précisément le problème | QQOQCCP, Analyse des données | Équipe multidisciplinaire |
D4 | Identifier les causes racines | Diagramme d’Ishikawa, 5 pourquoi, brainstorming | Experts techniques |
D7 | Standardiser la solution | Documentation qualité, procédures | Qualité / Opérations |
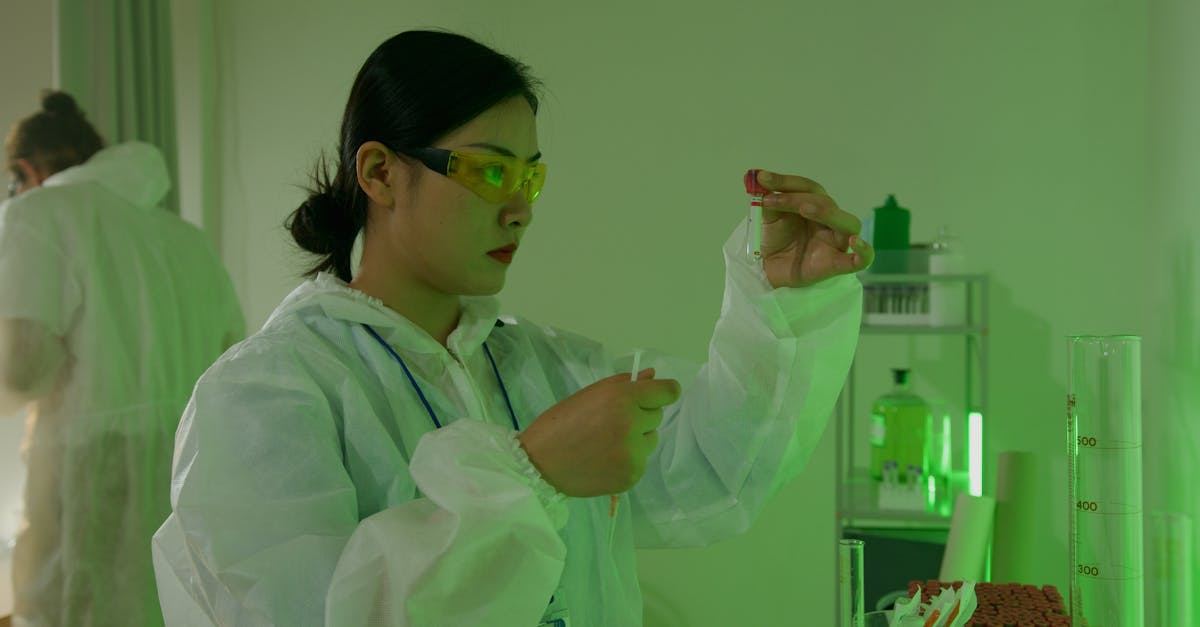
L’origine et l’évolution historique de la méthode 8D pour la résolution de problèmes efficaces
La provenance de la méthodologie 8D remonte aux années 1980, lorsque Ford Motor Company a développé cette démarche pour répondre à la nécessité croissante de résoudre des problèmes chroniques complexes en production et conception automobile. À cette époque, les solutions classiques ne garantissaient pas toujours la suppression durable des défauts. Ford a alors structuré un process en huit étapes disciplinées inspiré du cycle PDCA (Plan-Do-Check-Act) popularisé par Deming, pour formaliser la résolution des problèmes.
La méthode 8D a rapidement trouvé une application au-delà de l’automobile, intégrant les secteurs de l’aéronautique, la santé, la finance, et même les administrations publiques. Aujourd’hui, elle s’impose comme un standard reconnu mondialement, notamment dans le cadre des certifications ISO 9001 et des normes spécifiques à l’industrie automobile et manufacturière.
Son succès réside notamment dans son caractère collaboratif et itératif. Les équipes, en partageant leurs expertises, favorisent une meilleure analyse des causes du problème et établissent des solutions renforçant la qualité et la fiabilité. Dans une époque où la satisfaction client est devenue un indicateur clé de succès, la méthode 8D se positionne comme une méthodologie centrale en gestion de projet, garantissant une amélioration continue fiable et documentée.
Décennie | Évolution | Domaines d’application | Impact sur la gestion qualité |
---|---|---|---|
Années 1980 | Création par Ford Motor Company | Automobile | Formalisation de la résolution de problèmes |
Années 1990 | Adoption par autres industries | Aéronautique, santé, industrie manufacturière | Standardisation dans les certifications ISO |
Années 2000 à 2020 | Intégration aux méthodes d’amélioration continue | Finance, services, gouvernement | Consolidation du travail d’équipe et suivi des actions |
Années 2020 à 2025 | Digitalisation et optimisation via plateformes collaboratives | Multi-sectoriel durable | Performance renforcée et communication agile |
Étape clé D0 et D1 : préparation et constitution de l’équipe pour réussir la résolution de problèmes
Avant de s’engager dans la résolution détaillée d’un problème, il est indispensable de bien cadrer l’approche. Les étapes D0 et D1 de la méthode 8D posent les premiers jalons :
- D0 : Cette phase consiste à préparer le processus. Elle inclut la planification précise, la définition du périmètre du problème, le recensement des ressources nécessaires, et l’établissement d’un planning rigoureux. Le but est de s’assurer que tous les moyens nécessaires à une résolution efficace soient en place, ainsi que la mise en place de premières actions d’urgence pour limiter l’impact.
- D1 : L’étape suivante concerne la constitution d’une équipe multi-expertises qui prendra en charge l’identification, l’analyse et la résolution du problème. Cette équipe doit être composée de membres provenant de différents secteurs concernés (production, qualité, maintenance, management, etc.).
La réussite de ces phases conditionne fortement la performance du processus global. Un leader 8D est désigné pour assurer la coordination, motiver l’équipe et garantir le respect des objectifs.
Les bonnes pratiques à appliquer lors de D0 et D1 incluent :
- Définir explicitement l’objectif de résolution.
- Présenter clairement les enjeux au groupe.
- Assignation claire des responsabilités.
- Prévoir des temps de réunions réguliers pour assurer le suivi.
- Veiller à la disponibilité des ressources techniques et documentaires.
Étape | Actions spécifiques | Résultats attendus | Responsables |
---|---|---|---|
D0 | Planification, définition périmètre, allocation ressources | Processus cadré, ressources mobilisées | Management, chef de projet |
D1 | Sélection et mobilisation équipe pluridisciplinaire | Équipe opérationnelle définie | Leader 8D |
Développement approfondi sur les étapes D2 et D3 : analyser et circonscrire le problème efficacement
Les étapes D2 et D3 de la méthodologie 8D constituent le fondement de la compréhension du problème et de sa gestion immédiate :
- D2 – Description précise du problème : Il s’agit d’établir une fiche problème claire, exploitable et mesurable, en utilisant la méthode QQOQCCP. Cette étape est fondamentale pour cadrer parfaitement la problématique et éviter les maladresses dans l’analyse.
- D3 – Mise en œuvre des actions immédiates : Pour limiter les impacts, des actions de confinement doivent être déployées, telles que la mise en quarantaine de produits défectueux, l’information auprès des clients potentiellement affectés ou le remplacement provisoire de pièces ou processus défaillants.
Ces étapes exigent une collaboration exemplaire entre l’équipe et les parties prenantes, y compris le service client, pour la gestion des risques et de la perception de la qualité.
Voici une liste non exhaustive des points à détailler lors de D2 :
- Nature exacte du défaut ou problème.
- Quantité et fréquence du dysfonctionnement.
- Localisation géographique et temporelle.
- Impact sur les performances ou la sécurité.
- Identification des clients touchés ou segments de marché affectés.
Critères de description | Exemples | Outils utilisés |
---|---|---|
Qui | Client final, utilisateur interne | Analyse stakeholder |
Quoi | Défaut produit, erreur processus | Fiche problème, diagramme |
Où | Site usine, segment marché | Cartographie de processus |
Quand | Heure, période, fréquence | Analyse temporelle |
D4 et D5 : l’analyse des causes profondes et la mise en œuvre d’actions correctives durables
Ces étapes représentent le cœur de la méthodologie 8D en matière d’analyse des causes et résolution permanente :
- D4 – Identification des causes racines : Associer méthode rigoureuse et outils qualité pour remonter aux origines du problème. Le recours au brainstorming en équipe, au diagramme d’Ishikawa, et à la méthode des 5 pourquoi permet de cartographier les facteurs contributifs avec rigueur.
- D5 – Validation et implémentation des actions correctives : Une fois les causes établies, il est indispensable de concevoir des actions durables, validées en conditions réelles, notamment lors de pré-production ou tests physiques. Ces actions doivent éliminer définitivement le problème sans générer d’effets secondaires.
L’efficacité de ces phases conditionne le retour à la normale et la pérennité des résultats. Elles nécessitent aussi un suivi analytique et statistique fin, basé sur la collecte et l’interprétation de données concrètes.
Pour illustrer, voici des actions typiques associés à D4 et D5 :
- Révision des plans de fabrication.
- Modification des normes de contrôle qualité.
- Amélioration de la formation des opérateurs.
- Adaptation des matières premières ou fournisseurs.
- Automatisation des étapes critiques du processus.
ÉTAPE | DESCRIPTION | OUTILS | EXEMPLE D’ACTION |
---|---|---|---|
D4 | Analyse approfondie des causes racines | 5 pourquoi, Ishikawa, brainstorming | Changement fournisseur de pièce défectueuse |
D5 | Mise en œuvre actions correctives permanentes | Test pré-production, validation | Mise à jour procédure de contrôle qualité |
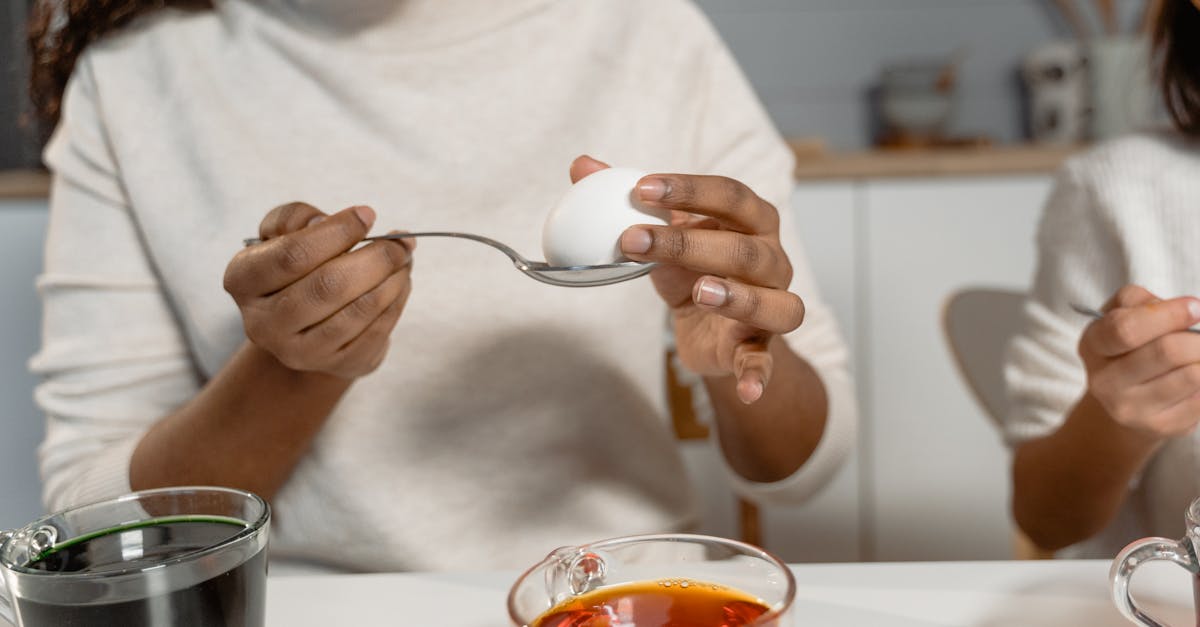
Étapes D6 et D7 : suivi de l’efficacité et standardisation pour assurer la pérennité
Assurer que les actions correctives ont pleinement résolu le problème est primordial. C’est l’enjeu des étapes D6 et D7 qui clôturent la partie opérationnelle :
- D6 – Mesure de l’efficacité : Collecte de données après mise en œuvre, suivi des indicateurs de performance et analyse comparative avec la situation initiale. L’objectif est d’identifier si le dysfonctionnement a disparu sans apparition d’effets négatifs secondaires.
- D7 – Standardisation et prévention : Intégration formelle des nouvelles pratiques dans les documents qualité, formation systématique des personnels concernés, audits réguliers pour vérifier le respect. Ces actions de standardisation deviennent partie intégrante du système de management pour garantir que le problème ne réapparaisse pas et éviter des dérives similaires.
Une collaboration étroite entre la qualité, les opérations, les ressources humaines et le management est essentielle pour réussir ces phases. Elles favorisent une véritable culture d’amélioration continue.
Étape | Objectifs | Méthodes | Livrables |
---|---|---|---|
D6 | Vérifier l’efficacité des actions correctives | Analyse des KPIs, comparaisons statistiques | Rapports d’efficacité |
D7 | Standardiser les améliorations | Documentation, formation, audit | Mises à jour des normes, procédures |
La finalisation avec D8 : valorisation du travail d’équipe et encouragement pour les succès futurs
La dernière étape, D8, souvent sous-estimée, est pourtant capitale pour renforcer la dynamique d’amélioration continue :
- Reconnaître les efforts : Un point de gratitude formel envers l’équipe permet de valoriser les compétences mobilisées et leur engagement.
- Motiver pour la suite : Cette reconnaissance est un moteur puissant pour encourager la collaboration future et l’investissement dans de nouveaux projets d’amélioration.
- Communiquer sur la réussite : Partager les résultats positifs en interne et auprès des clients renforce la confiance et la réputation de l’entreprise.
Fêter un succès collectif est une méthode efficace pour renforcer l’identité d’équipe et préparer le terrain pour aborder avec détermination les prochains défis qualité et gestion de projet.
Actions à engager | Objectifs | Moyens | Exemple |
---|---|---|---|
Reconnaissance officielle | Valoriser l’équipe | Réunion de clôture, courrier de remerciement | Remerciement par la direction |
Célébration | Renforcer la cohésion | Événement interne, sortie d’équipe | Repas collectif |
Communication externe | Partager les succès | Newsletter, réseaux sociaux | Publication d’un article sur la résolution |
Forces et limites de la méthode 8D : comment optimiser son usage dans la pratique
La méthodologie 8D bénéficie de plusieurs avantages indéniables qui en font un outil privilégié en gestion d’entreprise pour la résolution de problèmes :
- Meilleure compréhension des problèmes : En structurant l’analyse et la description du problème avec des données précises, elle élimine les approximations et oriente vers des solutions fondées.
- Collaboration multidisciplinaire : Le travail d’équipe diversifié génère des perspectives variées, enrichit le diagnostic et accroît la créativité.
- Amélioration durable : Par l’analyse des causes racines et la standardisation, elle s’inscrit dans une démarche d’amélioration continue pérenne et orientée vers la qualité globale.
Toutefois, la mise en œuvre de la méthode 8D présente des contraintes. Elle requiert du temps pour respecter chaque étape et impliquer pleinement une équipe souvent sollicitée sur d’autres tâches. De plus, il faut disposer d’une équipe pluridisciplinaire disponible et cohésive, ce qui peut poser problème selon les structures.
Pour optimiser l’usage de la méthodologie, il est conseillé de :
- Prioriser les problèmes en fonction de leur impact sur la satisfaction client et le business.
- Utiliser des outils digitaux adaptés pour faciliter le suivi des actions et la communication.
- S’appuyer sur des formations afin d’assurer un bon niveau de maîtrise de la méthode par tous.
- Intégrer la méthode 8D dans un système global de gestion de la qualité et d’amélioration continue.
Pour approfondir votre compréhension des systèmes de valeur et de leur optimisation complémentaire à la méthodologie 8D, consultez cet excellent article sur la chaîne de valeur.
Atouts de la méthode 8D | Limites à considérer | Solutions pour optimisation |
---|---|---|
Structure rigoureuse et claire | Processus long à mettre en œuvre | Planification détaillée et respect des délais |
Renforcement du travail d’équipe | Disponibilité variable des experts | Mobilisation de compétences clés, animations efficaces |
Standardisation et prévention | Complexité dans la mise à jour documentaire | Utilisation de logiciels adaptés pour la gestion documentaire |
FAQ sur la méthode 8D : réponse aux questions courantes pour les dirigeants et chefs de projets
- Qu’est-ce qui différencie la méthode 8D d’autres approches de résolution de problèmes ?
La méthode 8D se distingue par son processus rigoureux en huit étapes, insistant sur la collaboration multidisciplinaire, l’analyse des causes racines et la mise en place durable d’actions correctives, ce qui garantit une résolution complète et la prévention des récidives. - Comment former efficacement une équipe pour la méthodologie 8D ?
Il faut rassembler des membres aux compétences complémentaires, impliqués dans le produit ou le processus concerné, et nommer un leader capable de coordonner et mobiliser autour des objectifs précis et des délais fixés. - Quels outils sont recommandés pour l’analyse des causes profondes dans la méthode 8D ?
Les diagrammes d’Ishikawa, la méthode des 5 pourquoi, les brainstormings structurés, ainsi que les analyses statistiques et la matrice de priorisation sont incontournables pour une analyse fiable et exhaustive. - Comment assurer le suivi des actions correctives après leur mise en œuvre ?
L’utilisation d’indicateurs clés de performance pertinents, de rapports réguliers et d’audits internes permet d’assurer un monitoring efficace et d’ajuster les actions si nécessaire. - Peut-on appliquer la méthode 8D en dehors de l’industrie manufacturière ?
Absolument. Son approche systématique et collaborative est adaptable à tous secteurs, comme la finance, la santé, les services ou le secteur public, notamment pour améliorer la qualité et la satisfaction client.