Dans un environnement professionnel toujours plus concurrentiel et exigeant, comprendre les véritables causes des problèmes est devenu un atout majeur pour toute organisation. Le diagramme d’Ishikawa, aussi appelé diagramme en arêtes de poisson, s’impose comme un outil incontournable pour identifier les origines des dysfonctionnements tout en structurant une réflexion collective. Sa simplicité visuelle cache une puissance analytique capable de transformer la qualité des processus et d’impulser une amélioration continue, particulièrement prisée par des pionniers comme Toyota et Mitsubishi. En 2025, son intégration au sein des démarches Lean Manufacturing et Six Sigma reste une référence pour des cabinets stratégiques tels que Bain & Company, McKinsey & Company, Deloitte ou encore PWC, soulignant l’importance de cet outil dans la gestion moderne de la qualité et de la performance opérationnelle.
Les Fondements et la Structure du Diagramme d’Ishikawa : Clé de l’Analyse des Causes
Le diagramme d’Ishikawa est un outil graphique qui permet d’organiser et de visualiser les différentes causes potentielles d’un problème identifié. Il doit son nom à Kaoru Ishikawa, ingénieur japonais qui a conceptualisé cet outil dès les années 1960 pour améliorer la qualité dans les entreprises.
Sa forme distinctive, qui évoque l’arête dorsale d’un poisson, symbolise le cheminement des causes vers un effet central, souvent un problème ou un défaut spécifique. Cette représentation claire facilite l’air d’identification et le classement des facteurs contributifs, élément essentiel pour orienter les actions correctives.
La structure comporte trois niveaux essentiels :
- L’effet : situé à l’extrémité droite, il représente le problème ou la défaillance que l’on cherche à analyser.
- Les grandes catégories principales : illustrées par les arêtes principales du diagramme, elles regroupent les causes majeures. Traditionnellement, ces catégories s’appuient sur les 6M : Main-d’œuvre, Machines, Matières, Méthodes, Milieu et Mesures.
- Les causes secondaires : plus detailées, elles sont des sous-causes identifiées sous chaque catégorie principale, dans le but de cibler précisément les sources de défaillance.
Cette méthodologie encourage une analyse approfondie, allant au-delà des symptômes visibles du problème pour révéler ses racines véritables. Elle agit comme un révélateur de dysfonctionnements sous-jacents souvent ignorés dans les approches classiques.
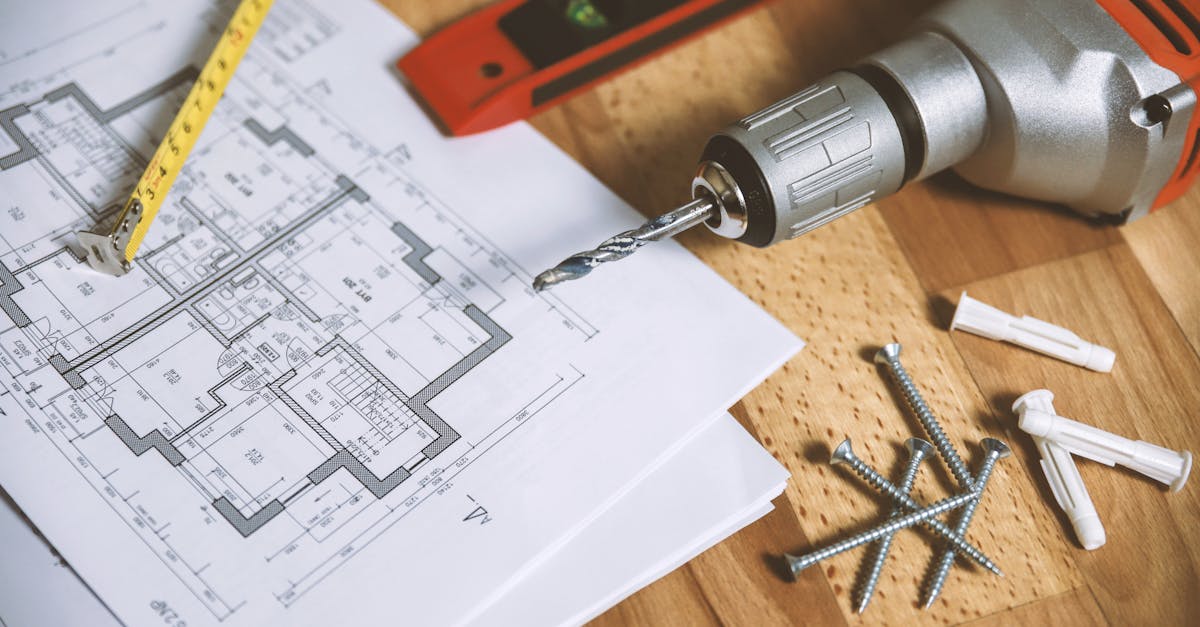
Une démarche standardisée pour une meilleure approche collective
Le diagramme est souvent construit lors de réunions de travail collaboratives, où les parties prenantes échangent leurs idées à travers un brainstorming rigoureux. L’avantage de ce format est d’associer des expertises variées pour une compréhension exhaustive de la problématique.
Dans des entreprises comme Mitsubishi, intégrant des démarches Lean Manufacturing, cette approche permet d’éviter les biais individuels et d’importer des réflexions multiples, ce qui est très valorisé dans les méthodes Six Sigma pratiquées.
Élément du diagramme | Description | Exemple d’application |
---|---|---|
Effet | Résultat problématique ou défaut à analyser | Défaut de production d’un composant électronique |
Grande catégorie (6M) | Regroupe les causes majeures | Machines : pannes fréquentes et obsolescence |
Cause secondaire | Détail des origines spécifiques | Manque de maintenance préventive |
Différentes versions du diagramme d’Ishikawa selon les besoins sectoriels
Si la version des 6M est la plus répandue, plusieurs déclinaisons du diagramme d’Ishikawa existent pour s’adapter aux contextes et objectifs spécifiques des entreprises.
Par exemple, le diagramme des 3M, très utilisé dans certaines petites unités de production ou ateliers, se concentre uniquement sur la Main-d’œuvre, les Machines et les Matériaux. Cette simplification permet une approche rapide lorsqu’il s’agit d’identifier des sources évidentes d’erreur ou de défaut.
À l’autre extrême, le diagramme des 8P élargit l’analyse à une perspective plus commerciale et organisationnelle :
- Procédures : qualité et clarté des instructions.
- Politiques : règles internes et directives.
- Place : localisation des opérations et contraintes associées.
- Produit : caractéristiques et adéquation au marché.
- Personnes : implication et compétences individuelles.
- Processus : étapes, enchaînement et suivi des activités.
- Prix : coûts, investissements, et marges.
- Promotion : stratégies de communication et marketing.
Cette déclinaison est notamment pertinente dans les stratégies de croissance, où l’analyse transverse permet d’intégrer qualité et performance financière. Des cabinets comme Deloitte ou PWC exploitent fréquemment cette approche pour conseiller leurs clients sur des problématiques multi-dimensionnelles.
Version du diagramme | Principales catégories | Domaines d’application typiques |
---|---|---|
3M | Main-d’œuvre, Machines, Matériaux | Ateliers de fabrication, petites équipes |
6M | Main-d’œuvre, Machines, Matières, Méthodes, Milieu, Mesures | Industrie manufacturière, contrôle qualité |
8P | Procédures, Politiques, Place, Produit, Personnes, Processus, Prix, Promotion | Marketing, gestion de produit, stratégie d’entreprise |
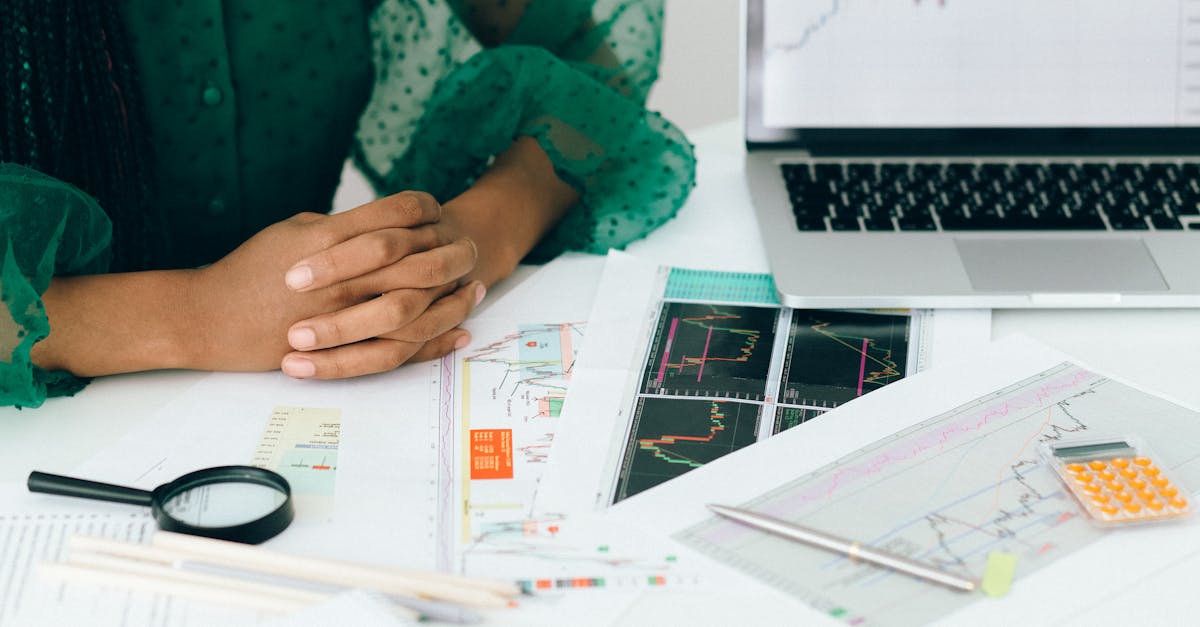
Étapes pratiques pour élaborer un diagramme d’Ishikawa performant avec Xmind
En 2025, tirer parti des outils digitaux est essentiel pour les professionnels cherchant à optimiser leurs analyses. Le logiciel Xmind, reconnu pour sa flexibilité, offre plusieurs modèles de diagrammes d’Ishikawa, facilitant grandement sa réalisation.
Voici un protocole éprouvé pour mener à bien sa construction :
- Définir le problème : Formuler clairement l’effet ou défaut à analyser, base incontournable d’une démarche efficace.
- Choisir la structure : Sélectionner parmi les modèles 3M, 6M ou 8P selon la complexité et le domaine d’étude.
- Déterminer les grandes catégories : Inscrire les branches principales qui représenteront les familles de causes.
- Brainstorming collaboratif : Questionner « Pourquoi ce problème survient-il ? » pour alimenter les branches secondaires avec les causes.
- Approfondir l’analyse : Poser plusieurs fois le « Pourquoi ? » afin d’explorer à des niveaux de détail supérieur.
- Annoter les causes prioritaires : Identifier celles qui ont le plus d’impact pour orienter les actions correctives.
- Explorer les zones moins remplies : Revenir sur les branches moins développées pour éviter les angles morts.
Cette méthode est largement utilisée par des sociétés impliquées dans les démarches Kaizen et Six Sigma, qui ont démontré l’importance de la précision dans la détection des causes pour améliorer la qualité et la productivité.
Étape | Description | Conseil professionnel |
---|---|---|
1 | Définir le problème | Assurez-vous que tout le groupe valide l’énoncé |
2 | Choisir la structure | Adaptez selon le secteur d’activité |
3 | Déterminer les catégories | Privilégiez des catégories claires et non redondantes |
4 | Brainstorming | Invitez tous les participants à exprimer leurs idées |
5 | Approfondir l’analyse | Utilisez la technique des « 5 Pourquoi » |
6 | Annoter les priorités | Marquez celles qui nécessitent une action immédiate |
7 | Explorer les zones moins remplies | Poussez la réflexion sur les causes moins évidentes |
Avantages stratégiques à intégrer le diagramme d’Ishikawa dans la gestion d’entreprise
Les bénéfices de cet outil vont bien au-delà d’une simple cartographie des causes. Il s’intègre parfaitement aux approches Lean Manufacturing et Six Sigma, permettant ainsi de réduire significativement les sources de défauts et d’optimiser la qualité.
- Identification claire et exhaustive : Visualiser toutes les causes potentielles dans un seul schéma aide à ne négliger aucune piste.
- Simplicité d’utilisation : Même les équipes non spécialisées en gestion de projet peuvent s’approprier rapidement l’outil.
- Encouragement à la collaboration : La méthode favorise la participation de toutes les parties prenantes, enrichissant la réflexion collective.
- Prise de décisions éclairée : Les causes prioritaires identifiées permettent de cibler précisément les interventions pour optimiser les résultats.
- Prévention des erreurs récurrentes : Comprendre en profondeur les raisons d’un défaut évite sa répétition, contribuant à la culture Kaizen.
Qualité Canada, par exemple, recommande cette approche dans ses formations pour développer une culture d’amélioration continue au sein des organisations canadiennes.
Avantages | Description | Impact opérationnel |
---|---|---|
Clarté | Visualisation holistique des causes | Diminution des erreurs par l’exhaustivité |
Accessibilité | Facilité d’utilisation pour tous | Rapidité d’adoption en entreprise |
Engagement collaboratif | Implication de multiples expertises | Analyse plus riche et pertinente |
Décisions ciblées | Priorisation des causes à traiter | Optimisation des ressources |
Culture d’amélioration | Réduction des erreurs répétitives | Performance durable améliorée |
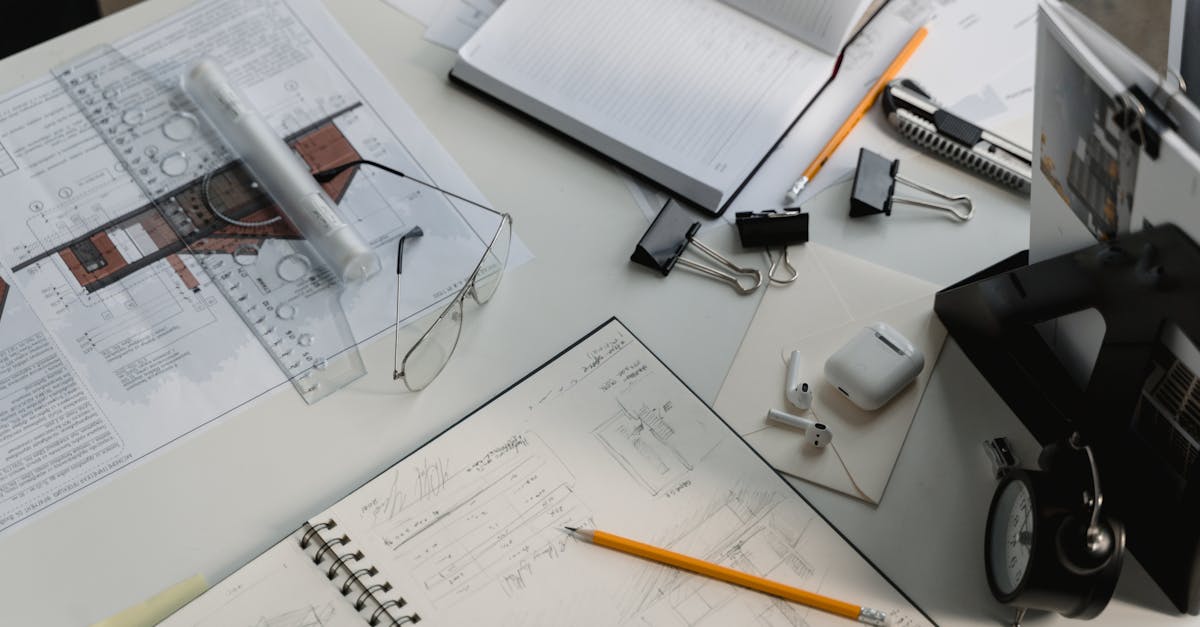
Applications sectorielles du diagramme d’Ishikawa : études de cas concrètes
La polyvalence du diagramme d’Ishikawa est attestée par ses usages dans divers secteurs qui valorisent la rigueur et la qualité.
Dans l’éducation, par exemple, les établissements l’utilisent pour analyser les obstacles à la réussite des étudiants et définir des plans d’actions personnalisés. Le diagramme met en lumière des facteurs comme les méthodes pédagogiques, les ressources disponibles, ou encore l’environnement d’apprentissage.
Dans le secteur manufacturier, en particulier chez Toyota, le diagramme s’inscrit au cœur des démarches Kaizen pour réduire les défauts sur les lignes de production. En identifiant précisément source après source, les ateliers peuvent mettre en œuvre des actions correctives ciblées, améliorant ainsi la productivité et la satisfaction client.
En matière de santé et sécurité au travail, le diagramme est employé pour analyser les accidents et incidents. Sa capacité à décomposer les causes en détail permet de concevoir des mesures préventives efficaces.
Secteur | Problème analysé | Exemple d’utilisation | Résultat attendu |
---|---|---|---|
Éducation | Obstacles à la réussite scolaire | Analyse des méthodes pédagogiques et ressources | Amélioration des performances étudiantes |
Manufacturier | Taux élevé de défauts sur production | Application Kaizen pour optimisation continue | Diminution significative des défauts |
Santé & Sécurité | Accidents du travail récurrents | Analyse des causes puis mesures préventives | Réduction des accidents |
Comment interpréter et prioriser les causes identifiées dans un diagramme d’Ishikawa
Après avoir construit un diagramme complet, l’étape suivante est cruciale : interpréter les données pour définir lesquelles des causes représentent le vrai levier d’amélioration.
Cette phase exige une analyse rigoureuse, notamment :
- Examiner la fréquence d’apparition d’une cause dans différentes catégories ou situations.
- Évaluer l’impact potentiel de la cause sur la qualité ou le processus.
- Considérer la faisabilité et les coûts liés à la correction des causes.
- Consulter les experts métiers pour valider les hypothèses avancées.
Une technique complémentaire est l’utilisation de la matrice de priorisation, qui croise l’importance et la faisabilité des interventions. Cette démarche efficace est utilisée dans les audits Lean Manufacturing et Six Sigma pour concentrer les efforts là où ils produiront le plus de bénéfices.
Critère | Description | Utilisation |
---|---|---|
Fréquence | Rapport de répétition du problème | Identification des causes récurrentes |
Impact | Gravité des conséquences possibles | Priorisation des causes critiques |
Faisabilité | Capacité à agir rapidement | Évaluation des ressources nécessaires |
Coût | Budget d’intervention | Planification selon coûts et bénéfices |
Des organisations comme Bain & Company recommandent toujours de baser la planification sur cette analyse pointue pour assurer une optimisation maximale sans gaspillage de ressources.
Exemples d’implémentation du diagramme d’Ishikawa dans la conduite de projets en 2025
Dans la gestion moderne de projets, le diagramme d’Ishikawa est un outil de prévention et de résolution qui garantit une meilleure maîtrise des risques et une exécution fluide.
Prenons l’exemple fictif d’une entreprise technologique qui voit son taux de satisfaction client baisser suite à des retards de livraison. En appliquant le diagramme, le chef de projet convient de plusieurs grandes catégories d’analyse, tel que les processus internes, l’équipe (main-d’œuvre), les technologies utilisées (machines), et les fournisseurs (matières).
- Dans Processus, on découvre des étapes redondantes et des délais non maîtrisés.
- Au niveau de la Main-d’œuvre, un manque de formation sur les outils numériques est identifié.
- Les Machines sont parfois obsolètes ou insuffisamment maintenues, provoquant des ralentissements.
- Les Fournisseurs connaissent des variations de qualité, impactant la production.
Le diagramme permet ainsi de voir clairement les pistes à suivre. L’entreprise investit dans des formations ciblées, optimise ses procédures, modernise certains équipements et instaure un contrôle qualité renforcé chez ses fournisseurs. Résultat, la satisfaction client se redresse rapidement et la productivité gagne en fluidité.
Catégorie | Cause identifiée | Action corrective | Résultat attendu |
---|---|---|---|
Processus | Étapes redondantes | Révision et optimisation | Gain de temps et fluidité |
Main-d’œuvre | Manque de formation | Programmes de formation numérique | Amélioration des compétences |
Machines | Obsolescence | Maintenance renforcée et modernisation | Réduction des pannes |
Fournisseurs | Variations de qualité | Renforcement des contrôles fournisseurs | Produits conformes attendus |
FAQ : Questions fréquemment posées autour du diagramme d’Ishikawa
- Quelles sont les limites d’un diagramme d’Ishikawa ?
Il peut devenir complexe dans le cadre de problématiques très vastes ou détaillées. Par ailleurs, il ne préconise pas automatiquement la priorisation des causes, ce qui nécessite une facilitation experte pour garantir l’efficacité de l’analyse. - Comment interpréter un diagramme d’Ishikawa ?
Après construction, il faut analyser en équipe chaque cause pour en évaluer la pertinence et l’impact. Cela permet d’orienter les actions sur les causes les plus critiques afin d’obtenir des résultats tangibles. - Le diagramme d’Ishikawa peut-il s’appliquer en dehors de l’industrie ?
Oui. Son emploi s’étend à des domaines divers tels que l’éducation, la santé, la gestion de projet ou le marketing, rendant cet outil polyvalent pour toute organisation soucieuse d’améliorer sa performance. - Quels sont les logiciels recommandés pour réaliser un diagramme d’Ishikawa ?
Xmind est particulièrement adapté, offrant des modèles simples à utiliser pour créer des diagrammes adaptés à chaque besoin professionnel. - Le diagramme d’Ishikawa sert-il uniquement à la résolution de problèmes ?
En plus de la résolution de problèmes, il est employé pour la prévention, la formation, et l’amélioration continue dans une logique Kaizen, soutenant ainsi la démarche Lean Manufacturing.